Structure of pneumatic butterfly valve
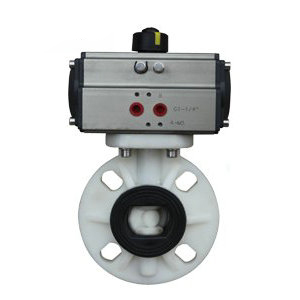
The purpose of these two eccentricities is the friction between the valve seat and the sealing ring during the valve switching stroke. The third eccentricity can be seen from Figure 2-30. The three eccentric structure has a larger eccentric angle than the double eccentric structure. The sealing surface of butterfly plate adopts eccentric cone. During the whole switching stroke of the valve, the butterfly plate and the sealing ring are separated from the geometry.
Most early pneumatic butterfly valves are sealed with natural rubber seats. Although it has excellent sealing performance, the applicable temperature and pressure are relatively low, usually around 70 ° C, no more than PN10. Later, synthetic rubber appeared and was applied to pneumatic butterfly valves to make the applicable temperature reach about 120 ℃ and the pressure reach PN16.
Corrosion resistance and abrasion resistance. Until today, it is still widely used in the water supply and drainage industry. With the rapid development of chemical industry and the emergence of fluoroplastics, the performance of pneumatic butterfly valves has been further improved. The pneumatic butterfly valve seat made of PTFE material makes the applicable temperature of the pneumatic butterfly valve as high as 180 ° C, the applicable pressure is relatively large, and it can withstand the corrosion of strong acids, strong alkalis and chemical solvents.
Due to the application of metal rigid sealing ring, metal sealing ring, metal elastic sealing ring, multi-layer stainless steel and graphite composite ring in the pneumatic butterfly valve, plus the eccentric butterfly plate structure, its edges are spherical, conical and other forms, similar to the metal elastic ring matching to form a tight sealing pair, so that the applicable pressure of the pneumatic butterfly valve is above PN63, and the applicable temperature is up to 600 ℃.